The Impact Of Reverse Logistics Supply Chain Technology
By Jim Dempsey, Panasonic System Solutions Company of North America
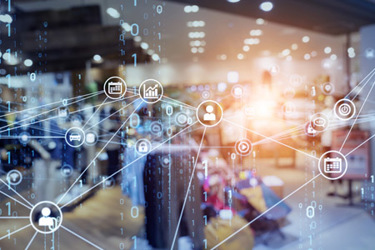
It is one thing for supply chain and logistics companies to bring a product from the manufacturer and warehouse to the customer, but it’s another thing to manage the process in reverse.
January and February always have been the “send-it-back” season for holiday gift returns. According to CBRE, in 2021 Americans spent a record $222 billion on online holiday purchases. Out of that, 30 percent will be sent back.
With reverse logistics technology, here is how companies can plan for an increase in returns and better manage the supply chain.
The Importance Of Reverse Logistics
A challenge most retailers face is that they do not have software or systems to determine the most efficient returns process or path to route the product.
For in-store returns, retailers need to leverage manual procedures that often leave room for error. For online returns, retailers rely on an inefficient reverse supply chain that routes items to multiple sites before reaching a returns center.
Reverse logistics is a critical component of the last mile as it directs products back to the warehouse, challenging companies to maintain visibility throughout their operations to streamline activities after the point of sale.
Having a plan for reverse logistics is necessary for companies to manage the tracking, collection, and shipping of returns, redeployment assets, or retired assets to the next or final destination. With mobile solutions deployed through the supply chain, mobile workers can manage returns with greater visibility to ensure a product arrives back to the manufacturer and warehouse. If reverse logistics is implemented carefully, retailers can strategically collect data, information, and reasons for the return.
Moving away from manual systems and providing supply chain workers with mobile, multi-modal solutions allows them to do their jobs more efficiently and with fewer errors.
Increasing Visibility At Every Step
Reverse logistics requires strategy, planning, and execution.
By incorporating the right technology at every touchpoint, the supply chain directs products back to the warehouse and maintains visibility throughout operations to streamline activities through the return.
With sensors and Internet of Things (IoT) technologies in delivery trucks, supply chain workers have more accurate in-transit visibility and robotics, sensors, and edge devices enable a seamless return process at each step.
The reverse logistics process includes the following steps:
- Processing the return: Reverse logistics starts with the consumer signaling a return, which involves scheduling return shipments, approving refunds, and replacing damaged goods.
- Dealing with the return: When a product returns to the warehouse, supply chain workers must inspect it and determine its return category. For example, resell as new, resell as a return, recycle, or refurbish.
- Keeping the product moving: Reduce any bottlenecks by sending products to their appropriate departments.
- Check for damages: After reviewing a returned item, determine whether it can be repaired and resold.
- Recycle the product: Once a product is inspected, any parts or products that cannot be resold can potentially be sent to an area for recycling.
With location-based data, warehouses can leverage real-time information about the flow of goods into the facility and direct products to the next phase of the chain.
Managing The Supply Chain
There are a lot of moving pieces in the supply chain.
Today, retailers and supply chain professionals need to have a plan in place to minimize waste and cut down on inefficiencies in reverse logistics.
Technology has the power to be the unifying link that closes the operational gaps – especially as warehouses experience a high volume of products moving from both ends of the supply chain.
About The Author
Jim Dempsey is director of U.S. business development and partnerships, which focuses on identifying, recruiting, and managing strategic relationships to broaden Panasonic mobility’s presence in existing and emerging business verticals. He has worked for Panasonic since 2011 in various roles including director of the TOUGHBOOK EDGE Authorized Mobility Partner Program, business development manager, and national manager of the Mobility Partner Development Group.